Coatings
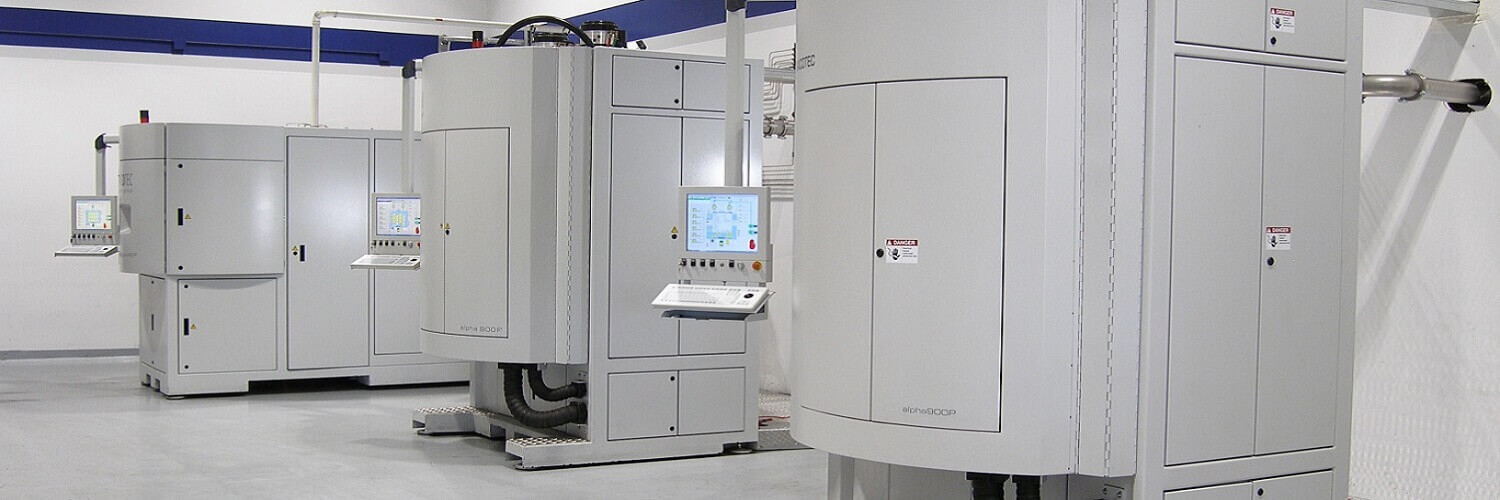
BÖHLER USA can offer coatings via its sister company voestalpine eifeler Coatings which is home to state of-the-art Physical Vapor Deposition (PVD) coatings center, equipped with the latest in PVD coating process technology. PVD is a vacuum coating technique, which creates a film on the surface of the required material to maintain its hardness. The film improves part quality, creates higher productivity, and increases tool life. A major benefit of PVD coating is its use of low temperature during the procedure, which avoids distortions in the tool.
eifeler´s PVD coating centers specializes in creating custom coatings for the automotive, die casting, aerospace and plastic injection tooling industries, but is committed to accommodate a wide range of customer needs.
The coating centers works side by side with the BÖHLER steel division to offer our customers a complete solution – we are able to advise on an application with material selection, heat treatment specifications and coating technology.
At BÖHLER, we are devoted to providing on-time delivery, competitive prices for high performance coatings and exceptional customer service.